Large connector behind gauge cluster, had to relocate some pins in order to use the old connector, and the turbo indicator plug had to get switch over.
The pins didn't fit the newer connector so i soldered it and heatshrink after:
Additional plugs by kick panel to be switched to newer year plug style
Other news, I helped SupraStroker88 with his Santa Cruz supra, its running now YAY
Harness needed repair: remove scotch-loks, replace couple plugs
He got a real deal on this supra, the guy just wanted it gone and anything related.
Hooking up the starter, I peeped this:
What clutch is on there too, I don't know still
My GF has a nice country location now. I get to see the hills in the morning
This is a prime example of literal meaning behind "Golden Hills of California".
They are green about 5 weeks of the year, around February/March.
I absolutely love when its green, the way the oak trees stand out on the round hills.
I've been meaning to photo shoot it with the Supra for YEARS now but its always one thing or another holding me up plus the short time window.
MY Supra progress:
Been sourcing prime wires to use for the after market gauges and Accusump EPC.
Driver kick panel fuse location 8 has a blank I'll be removing for a custom harness to plug in with a few inline fuses to supply the daisy chain of gauges with full time 12v+ and the EPC switch.
Hmm that makes me realize the EPC switch oughta to get power from my ACC 12v+ choice: The Red/Blue (R-L) of the cig lighter plug.
Full-time 12v+ for Prosport Premium gauges (memory for peak I believe, illumination color is chosen by wire) from kick panel fuses
ACC 12v+ for EPC and gauges from R-L cig plug wire.
Illumination wire for gauges from G(reen) at Foglight switch plug.
Ground for gauges is from W-B of Foglight switch.
That's the last of the wiring necessary to run at the moment.
Later is the WBo2 and maft-pro, both of which already have leads prepared by the ECU for future install.
Ever closer.
You know what, I dunno how IJ. makes such fast progress. Ever notice how fast he moves day to day? He must be smarter or something (ignore the experience factor please lol)
I plan on mounting the gauges on the steering column. The issue is there will be 5 gauges and I dunno how they'll fit. Custom column cover perhaps?
Obviously I'm avoiding conventional locations.
A-pillar mounting is a bit rice-and-lifted-diesel-truckish around here.
I don't really care for hacking into my gauge panel.
Glove box is far. It should be closed during driving too
The stereo and climate controls aren't moving, and I need my cig lighter for those plug in goodies like GPS and phone charger.
Lining the top of the dash with gauges, it sounds ok but I'd rather not drill my dash or be that obvious.
Sounds like this will be interesting hehe
Edit:
Yes I know solder joints die fast in a car. Wanna know why? The wires got over heated, or too much flux ran up the strands and didn't burn off cuz its under the insulation.
Its true that soldering makes the wire more brittle where the solder ends but the same is true about welding.
Proper crimps are longer term, but good wire solder joints aren't that hard.
Pointers on wire soldering:
- a CLEAN tip of your soldering iron really helps. Wipe it off on a wet sponge after every joint.
- a "Helping Hand" is worth the money (alligator clips on an adjustable stand)
- strip enough wire insulation so it doesn't melt.
- put the appropriate sized heat shrink tubing on before the next step
- twist and j-hook the wires to interlink for easier working of the joint.
- I find it easier to melt a ball of flux cored solder onto the iron tip and then heat up the wires with the wet ball.
- Bigger wires mean more heat/power and larger gauge solders. My 35W iron isn't that great for bigger than 14awg. There comes a point where crimping is more time efficient/RELIABLE, usually 8awg and larger.
- When the joint is melting the solder, I add solder at the intersection of the iron and existing wet solder under the wire, to burn off the excess flux. Enough flux will wick from that location down the strands. Only move the solder on top of the "wet" joint if there's not enough coverage.
- "Enough" is the point where the joint's strands and a bit of the wires up to the joint are coated. You still want to see the shape of the strands when your done.
- Cool ambient temperature and wind will affect the time it takes to heat up the wires. Avoid wind.
I'm a perfectionist. I'm always experimenting if I don't feel something is correct. And I like hearing other opinions as there's more than one way to cut down a tree
The pins didn't fit the newer connector so i soldered it and heatshrink after:
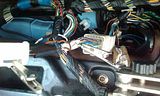
Additional plugs by kick panel to be switched to newer year plug style
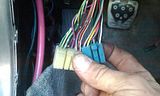
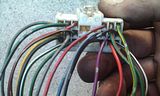
Other news, I helped SupraStroker88 with his Santa Cruz supra, its running now YAY
Harness needed repair: remove scotch-loks, replace couple plugs
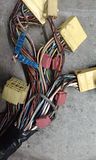
He got a real deal on this supra, the guy just wanted it gone and anything related.
Hooking up the starter, I peeped this:
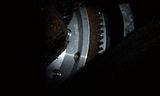
What clutch is on there too, I don't know still
My GF has a nice country location now. I get to see the hills in the morning
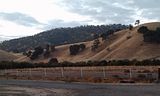
This is a prime example of literal meaning behind "Golden Hills of California".
They are green about 5 weeks of the year, around February/March.
I absolutely love when its green, the way the oak trees stand out on the round hills.
I've been meaning to photo shoot it with the Supra for YEARS now but its always one thing or another holding me up plus the short time window.
MY Supra progress:
Been sourcing prime wires to use for the after market gauges and Accusump EPC.
Driver kick panel fuse location 8 has a blank I'll be removing for a custom harness to plug in with a few inline fuses to supply the daisy chain of gauges with full time 12v+ and the EPC switch.
Hmm that makes me realize the EPC switch oughta to get power from my ACC 12v+ choice: The Red/Blue (R-L) of the cig lighter plug.
Full-time 12v+ for Prosport Premium gauges (memory for peak I believe, illumination color is chosen by wire) from kick panel fuses
ACC 12v+ for EPC and gauges from R-L cig plug wire.
Illumination wire for gauges from G(reen) at Foglight switch plug.
Ground for gauges is from W-B of Foglight switch.
That's the last of the wiring necessary to run at the moment.
Later is the WBo2 and maft-pro, both of which already have leads prepared by the ECU for future install.
Ever closer.
You know what, I dunno how IJ. makes such fast progress. Ever notice how fast he moves day to day? He must be smarter or something (ignore the experience factor please lol)
I plan on mounting the gauges on the steering column. The issue is there will be 5 gauges and I dunno how they'll fit. Custom column cover perhaps?
Obviously I'm avoiding conventional locations.
A-pillar mounting is a bit rice-and-lifted-diesel-truckish around here.
I don't really care for hacking into my gauge panel.
Glove box is far. It should be closed during driving too
The stereo and climate controls aren't moving, and I need my cig lighter for those plug in goodies like GPS and phone charger.
Lining the top of the dash with gauges, it sounds ok but I'd rather not drill my dash or be that obvious.
Sounds like this will be interesting hehe
Edit:
Yes I know solder joints die fast in a car. Wanna know why? The wires got over heated, or too much flux ran up the strands and didn't burn off cuz its under the insulation.
Its true that soldering makes the wire more brittle where the solder ends but the same is true about welding.
Proper crimps are longer term, but good wire solder joints aren't that hard.
Pointers on wire soldering:
- a CLEAN tip of your soldering iron really helps. Wipe it off on a wet sponge after every joint.
- a "Helping Hand" is worth the money (alligator clips on an adjustable stand)
- strip enough wire insulation so it doesn't melt.
- put the appropriate sized heat shrink tubing on before the next step
- twist and j-hook the wires to interlink for easier working of the joint.
- I find it easier to melt a ball of flux cored solder onto the iron tip and then heat up the wires with the wet ball.
- Bigger wires mean more heat/power and larger gauge solders. My 35W iron isn't that great for bigger than 14awg. There comes a point where crimping is more time efficient/RELIABLE, usually 8awg and larger.
- When the joint is melting the solder, I add solder at the intersection of the iron and existing wet solder under the wire, to burn off the excess flux. Enough flux will wick from that location down the strands. Only move the solder on top of the "wet" joint if there's not enough coverage.
- "Enough" is the point where the joint's strands and a bit of the wires up to the joint are coated. You still want to see the shape of the strands when your done.
- Cool ambient temperature and wind will affect the time it takes to heat up the wires. Avoid wind.
I'm a perfectionist. I'm always experimenting if I don't feel something is correct. And I like hearing other opinions as there's more than one way to cut down a tree
Last edited: