Wish you were closer.
I would offer to help you out with this.
Don't think it's the gears causing the noise, something is off somewhere.
Without seeing it in my hands I couldn't tell you where the error is.
Your setup and build notes look ok to me, my guess is something is off with the bearings / preload or the procedure it was setup.
Don't think bearings are bad.
A well setup diff makes no noise, notta / zilch.
I've had mine to 130 mph and everywhere in-between, totally dead silent.
Same goes for the others I have built and shipped out.
One exception is the MKIII diffs, they have an inherent resonant frequency they hit around 45-50mph.
Ive been able to mitigate it somewhat with REM polishing on the gears and bearings, but never fully goes away.
Just a design flaw / harmonic it hits.
For the backlash difference have you checked the runout of the LSD center?
( The flat face the gearset bolts to)
Curious what would drive that large of a difference in backlash, unless the gears were not machined properly.
Thanks Piratetip. I have not checked the open diff carrier center, but I did check the China ring gear runout and it was only 0.03mm maximum, well under the 0.1mm allowed. I still believe it is the ring and pinion based on 4 reasons.
1. The previous rebuild with the old gears had no noise on accel, only decel. I have not altered any other component .
2. The Backlash variation on this new China ring and pinion is just too much, from 0.24mm max, to 0.06mm min. It's not ring gear runout, either the ring gear tooth are not consistent, OR its the pinion cut that not consistent, I tend to think its the pinion cut.
3. Perhaps this new gear that is originally for a landcruiser from the 80's has a different height centerpoint (center of ring gear to pinion axis) ,compared to the mk3 supra housing. I say this because I went deep and shallow on the pinion depth, but only the drive side pattern is changing, the coast side seem to have no change ! That is very odd to me.
4. The noise is now on accel and decel, still worse on decel, and if i go very slow, I can hear the alternating intensity of the sound, the faster I go the sound is like "one coherent unit", and if very slow, its cyclical or position based. This time the noise is not a knock but a "grind", kinda like when you use a grinding stone.
I agree about the hum at 45 - 50mph, but that is totally acceptable and hardly noticable unlike the issue I have now.
So here is my plan, as I can't just leave this be, it's just who I am. I am getting old at 46 years old now, but I still have that "fire" in me to get this done. The only "good" thing about all this I am now able to remove and reassemble the diff , as well as take apart and put everything back much faster than ever, while still being careful. I have gotten used to the diff internals and the procedures intimately over the course of these 2 months.
1. I am now trying to source OEM gears from Toyota
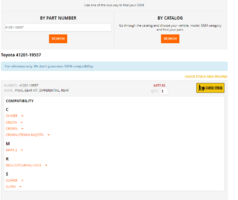
I will be making a purchase within this week, waiting time for toyota to make this part is 3 weeks, plus another week and half to pack and ship to me.
I am told the OEM gears are lapped as a pair before sending out, and this set is definitely meant for this housing. It's expensive, but I just dont have the time to fool around anymore.
2. I will get one 2.58mm shim, the thinnest one, just in case I need it, the pinion head shims, I should have them all this week.
3. This time I will insert the carrier center without ring gear and check it's runout.
4. This last point is very important, I need to find a way to test the diff before reassembling to the car. I was thinking of using the sockets and connectors for the inch-lb torque wrench and connecting it to a drill to turn the input flange on the diff and see If I can replicate the sound on the diff before I take it apart. At least if the sound is there when I do this, after another rebuild I can run this test and see if the sound is gone.
Yes, I would rather not do this, and pay some one like you, but to ship a 38kilo diff to the US by air would cost more than your asking fee for sure.
Btw, do you see anything wrong about this pinion head bearing ?
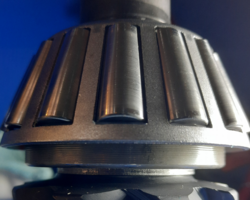
I see "scuff" marks on the rollers, I think I will just replace the bearing and shell as cheap security, since the pinion yoke bearing is brand new.