I didn't want to further hijack HKS_TRD's build thread ( http://www.supramania.com/forums/showthread.php?t=68023 ) so I'll try to move the discussion here.
When your car overheats, there is a good chance the cylinder head will warp. This generally happens because of uneven temperatures across the head (such as a blown head gasket on cylinder 5 or 6). The hotter a metal gets, the easier it is to bend.
The TSRM specifies a maximum warpage of .0039" (0.1mm) across any of the 9 measurement points shown in step 6:
If you were to just machine this head and slap on a new head gasket, you would end up with something like this awesome MSpaint drawing (exaggerated for effect):
The bottom of the head is flat, and will usually seal just fine. However, more material was removed from the center of the head than the ends, so the compression would end up slightly higher in the middle cylinders than the end. That could probably be lived with, but what makes this so bad is that the cam will now be forced to bend. This creates a lot more drag on the engine, can cause significant vibration, and will eventually cause uneven wear on the cam bearings and journals. Taken to excess, this could even lead to a seized engine and/or cam breakage.
Toyota would like you to simply discard your head and buy a new one (MSRP $1550 at the time of this writing -- ~$1275 from discount dealers). You could also try and find a used head and hope it checks out ok.
But in many cases, it is possible for a good machine shop with specialized tools and training to straighten a head back into spec. This procedure generally costs $200-$300 though it also comes with the risk of annealing your head. If you don't have a lot of money tied up in existing portwork I'd recommend trying to find a good core first (I've found 7m heads from Cressidas and NA Supras are the best bet). But if you can't find a good core or you've already spent a lot of time and money with your existing head, then straightening can be a good option. I just think its important to understand the processes and risks with the various procedures:
Oven heat: This is by far the most common method, and most good machine shops have the equipment and are knowledgeable in the risks and procedure. The basic idea is to locate the warp in the head, and physically bend the head in a matter that compensates for the warp. The head is then put in an oven, and heated to 400-500 degrees F for about 2 hours. At this point, the head should be straight. The key is to have an experienced technician who can get this done the first time. The longer a head bakes, the more annealing the aluminum goes through so if this process requires the head to be in the oven for 6+ hours at 450 degrees you increase the risk of having unacceptably soft head.
Video showing the process: http://www.youtube.com/watch?v=HlCrkytRwls&feature=player_embedded
Torch: This is a low tech procedure, but it requires a lot more skill and experience. Basically the head is mounted on shims to force it straight just like with oven-heating, but instead of having to put the entire head in an oven for 2 hours -- the technician uses a torch to heat just the right places on the head to bend it back straight. The advantage here is that any annealing will be localized to areas where having a softer material doesn't matter. The risk is that an inexperienced technician can easily ruin a head by applying too much heat to the wrong places.
Here is a very good article from an engine building magazine goes into detail on the risks of various procedures: http://www.enginebuildermag.com/Art...r_head_straight_about_head_straightening.aspx
So what is annealing, and why is it bad for a cylinder head?
There is a lot of science behind annealing, but the general idea is that at elevated temperatures, metal's crystal structure will change in a manner that brings the material into a more relaxed state. The result is a finished product that is softer, more bendable (less brittle), and has less tensile strength:
In many cases, this is desirable (less prone to cracking/snapping) but for a cylinder head, the loss in hardness/tensile strength can lead to studs pulling out of the head or, in the worst case, valve seats falling out.
Yet annealing is generally a slow process -- one that depends on time and temperature. Here is a chart that shows what happens to the tensile strength of 6061-T6 aluminum alloy after being baked at a various temperatures over time:
After 1/2 hour at 400 degrees, 6061 still has ~95% of its initial tensile strength. After 10 hours, it has ~85% of its initial tensile strength. But if we heat it to 500 degrees instead, 6061 has just 74% of its tensile strength after 1/2 hour and 48% after 10 hours. When fully annealed, 6061 only has ~ 20% of its initial strength (a process that takes >10 hours at 700 degrees).
Anyway its clear that the temperature is critical, and that as little heat/time as possible should be spent annealing -- so it really is crucial that you find a good, experienced shop.
A note about hardness/tensile strength: These properties are very closely related and I've probably used the terms interchangeably. Most shops will refer to the hardness of a head simply because a hardness test is how they will measure the tensile strength. Here's a quick link that goes into a little more detail: http://www.calce.umd.edu/general/Facilities/Hardness_ad_.htm
Going back to our processes -- your typical oven-heat method will be 400-500 degrees for less than 2 hours. As mentioned in the article, the good shops are keeping the temperature down around 425. Doing so will typically only reduce the hardness 5-7% -- an acceptable amount. The torch method will probably be more like 600 degrees for just a few seconds at specific locations. This might reduce hardness at those points by 10-15% -- but as long as the affected areas are not critical the integrity of the overall head will remain intact.
But wait -- EGTs in the manifold can reach 1300 degrees (and 1500+ degrees inside the combustion chamber) -- doesn't this anneal the head as well? Yes, it does. If you've ever ported a head before, you may have noticed how much easier the exhaust ports are to work with initially. This is because the surface has been pretty well annealed, but its effect decreases as you move further into the metal. Still, the exhaust side of heads is generally softer (why it is common for exhaust studs to pull out on 7m's).
But as many people have shown, after helicoiling the exhaust stud holes (or using timeserts - -for Howard
) their head is perfectly fine and ready to last another 150,000+ miles. Remember that exhaust ports don't need to have all of their original hardness/strength to properly function. Still, you can help prevent this effect by thermal coating the combustion chamber and exhaust ports, insulating the aluminum from the heat to prevent further annealing (swaintech is one of many companies that will do this: http://www.swaintech.com/store.asp?pid=10322 )
Annealing isn't something that is accomplished instantly -- its not an on/off switch. An overheating head might warp in less than a few minutes -- certainly not enough time to appreciably anneal the whole head. But you're right that any of the straightening procedures will further anneal the head -- the question is just how much hardness/strength is lost and whether that loss is acceptable. 10% or less, and I'm perfectly happy running the head again.
Sounds like they either used too much temperature (or way too much time), your head was badly warped, and/or the previous owner was a numbnut who overtorqued everything. In any case, I probably wouldn't feel comfortable using your head and would start looking for a core. If it was just the exhaust studs I'd happily run it. But if it was as widespread as it seems, I just think the chances of dropping a valve seat are unacceptable imo.
When your car overheats, there is a good chance the cylinder head will warp. This generally happens because of uneven temperatures across the head (such as a blown head gasket on cylinder 5 or 6). The hotter a metal gets, the easier it is to bend.
The TSRM specifies a maximum warpage of .0039" (0.1mm) across any of the 9 measurement points shown in step 6:

If you were to just machine this head and slap on a new head gasket, you would end up with something like this awesome MSpaint drawing (exaggerated for effect):

The bottom of the head is flat, and will usually seal just fine. However, more material was removed from the center of the head than the ends, so the compression would end up slightly higher in the middle cylinders than the end. That could probably be lived with, but what makes this so bad is that the cam will now be forced to bend. This creates a lot more drag on the engine, can cause significant vibration, and will eventually cause uneven wear on the cam bearings and journals. Taken to excess, this could even lead to a seized engine and/or cam breakage.
Toyota would like you to simply discard your head and buy a new one (MSRP $1550 at the time of this writing -- ~$1275 from discount dealers). You could also try and find a used head and hope it checks out ok.
But in many cases, it is possible for a good machine shop with specialized tools and training to straighten a head back into spec. This procedure generally costs $200-$300 though it also comes with the risk of annealing your head. If you don't have a lot of money tied up in existing portwork I'd recommend trying to find a good core first (I've found 7m heads from Cressidas and NA Supras are the best bet). But if you can't find a good core or you've already spent a lot of time and money with your existing head, then straightening can be a good option. I just think its important to understand the processes and risks with the various procedures:
Oven heat: This is by far the most common method, and most good machine shops have the equipment and are knowledgeable in the risks and procedure. The basic idea is to locate the warp in the head, and physically bend the head in a matter that compensates for the warp. The head is then put in an oven, and heated to 400-500 degrees F for about 2 hours. At this point, the head should be straight. The key is to have an experienced technician who can get this done the first time. The longer a head bakes, the more annealing the aluminum goes through so if this process requires the head to be in the oven for 6+ hours at 450 degrees you increase the risk of having unacceptably soft head.
Video showing the process: http://www.youtube.com/watch?v=HlCrkytRwls&feature=player_embedded
Torch: This is a low tech procedure, but it requires a lot more skill and experience. Basically the head is mounted on shims to force it straight just like with oven-heating, but instead of having to put the entire head in an oven for 2 hours -- the technician uses a torch to heat just the right places on the head to bend it back straight. The advantage here is that any annealing will be localized to areas where having a softer material doesn't matter. The risk is that an inexperienced technician can easily ruin a head by applying too much heat to the wrong places.
Here is a very good article from an engine building magazine goes into detail on the risks of various procedures: http://www.enginebuildermag.com/Art...r_head_straight_about_head_straightening.aspx
So what is annealing, and why is it bad for a cylinder head?
There is a lot of science behind annealing, but the general idea is that at elevated temperatures, metal's crystal structure will change in a manner that brings the material into a more relaxed state. The result is a finished product that is softer, more bendable (less brittle), and has less tensile strength:

In many cases, this is desirable (less prone to cracking/snapping) but for a cylinder head, the loss in hardness/tensile strength can lead to studs pulling out of the head or, in the worst case, valve seats falling out.
Yet annealing is generally a slow process -- one that depends on time and temperature. Here is a chart that shows what happens to the tensile strength of 6061-T6 aluminum alloy after being baked at a various temperatures over time:
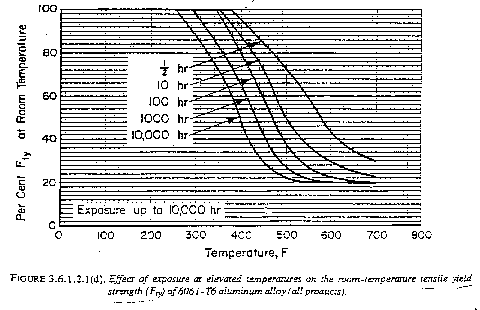
After 1/2 hour at 400 degrees, 6061 still has ~95% of its initial tensile strength. After 10 hours, it has ~85% of its initial tensile strength. But if we heat it to 500 degrees instead, 6061 has just 74% of its tensile strength after 1/2 hour and 48% after 10 hours. When fully annealed, 6061 only has ~ 20% of its initial strength (a process that takes >10 hours at 700 degrees).
Anyway its clear that the temperature is critical, and that as little heat/time as possible should be spent annealing -- so it really is crucial that you find a good, experienced shop.
A note about hardness/tensile strength: These properties are very closely related and I've probably used the terms interchangeably. Most shops will refer to the hardness of a head simply because a hardness test is how they will measure the tensile strength. Here's a quick link that goes into a little more detail: http://www.calce.umd.edu/general/Facilities/Hardness_ad_.htm
Going back to our processes -- your typical oven-heat method will be 400-500 degrees for less than 2 hours. As mentioned in the article, the good shops are keeping the temperature down around 425. Doing so will typically only reduce the hardness 5-7% -- an acceptable amount. The torch method will probably be more like 600 degrees for just a few seconds at specific locations. This might reduce hardness at those points by 10-15% -- but as long as the affected areas are not critical the integrity of the overall head will remain intact.
But wait -- EGTs in the manifold can reach 1300 degrees (and 1500+ degrees inside the combustion chamber) -- doesn't this anneal the head as well? Yes, it does. If you've ever ported a head before, you may have noticed how much easier the exhaust ports are to work with initially. This is because the surface has been pretty well annealed, but its effect decreases as you move further into the metal. Still, the exhaust side of heads is generally softer (why it is common for exhaust studs to pull out on 7m's).
But as many people have shown, after helicoiling the exhaust stud holes (or using timeserts - -for Howard
GC89;1341245 said:The problem is once aluminum gets hot enough to warp it anneals, so heating it again is just ensuring its compromised. It may be straight but its soft and not worth using.
Annealing isn't something that is accomplished instantly -- its not an on/off switch. An overheating head might warp in less than a few minutes -- certainly not enough time to appreciably anneal the whole head. But you're right that any of the straightening procedures will further anneal the head -- the question is just how much hardness/strength is lost and whether that loss is acceptable. 10% or less, and I'm perfectly happy running the head again.
Poodles;1340990 said:Shop did that to my head... had to use the larger upgrade size helicoils for the exhaust and it ended up stripping spark plug threads...
Something tells me they fucked up...
Sounds like they either used too much temperature (or way too much time), your head was badly warped, and/or the previous owner was a numbnut who overtorqued everything. In any case, I probably wouldn't feel comfortable using your head and would start looking for a core. If it was just the exhaust studs I'd happily run it. But if it was as widespread as it seems, I just think the chances of dropping a valve seat are unacceptable imo.
Last edited: