I have a bolt-on 62-1 Turbonetics T4 (look at avatar) that has ports for both oil and coolant. The issue I have is, the previous owner of my engine never ran coolant to his turbo's and welded up the coolant outlet on the engine.
When I called him and asked if I could route the coolant from somewhere else, he told me not to even bother, leave the coolant port on the turbo open, and that he never runs coolant on any of his turbo's. His theory is that turbo's only house roughly 3 ounces of coolant and that coolant runs hotter than oil anyways. The guy races supra's all the time and even owns his own dyno shop, so I wasn't going to argue with him.
If I don't run coolant, will it harm the turbo and/or hinder performance. I figure if the turbo has a port for coolant, it was obviously designed to run coolant for a reason.
So what say you, am I better off just running no coolant at all? Otherwise, what's the best way for me to route coolant to the turbo now that the engine coolant outlet is welded shut?

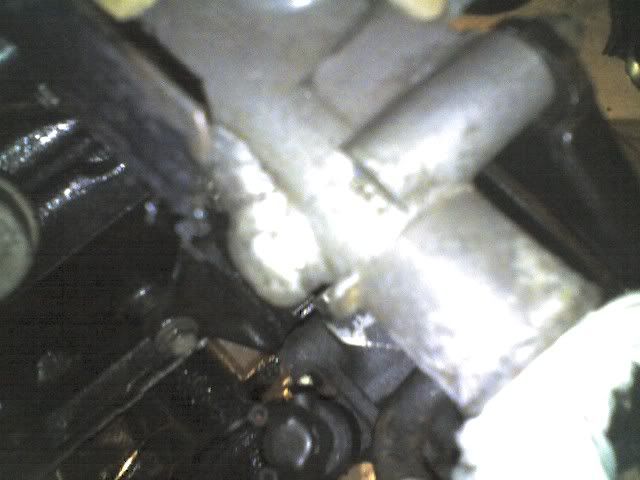
When I called him and asked if I could route the coolant from somewhere else, he told me not to even bother, leave the coolant port on the turbo open, and that he never runs coolant on any of his turbo's. His theory is that turbo's only house roughly 3 ounces of coolant and that coolant runs hotter than oil anyways. The guy races supra's all the time and even owns his own dyno shop, so I wasn't going to argue with him.
If I don't run coolant, will it harm the turbo and/or hinder performance. I figure if the turbo has a port for coolant, it was obviously designed to run coolant for a reason.
So what say you, am I better off just running no coolant at all? Otherwise, what's the best way for me to route coolant to the turbo now that the engine coolant outlet is welded shut?